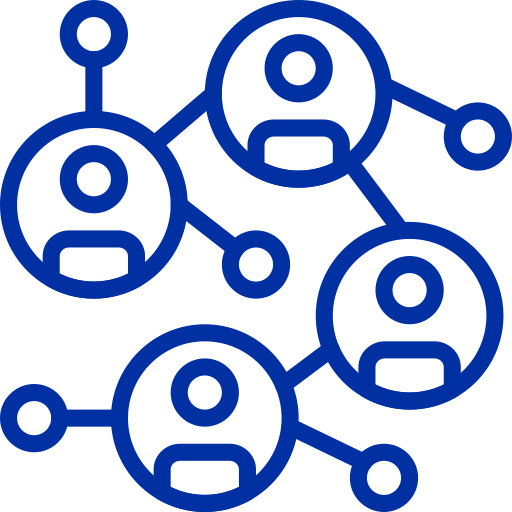
Supply Chain :
Zoitech strives to aid customers by optimizing costs and cutting downtime in electronics production by consolidating electronic supply chain solutions and value engineering.
We render our material sourcing and contract manufacturing services to mechanical, electrical, electronic components, sub-assemblies, and other varied industries.
To aid life cycle management our team offers electronic sourcing services comprising of
- Value analysis
- Vendor evaluation
- Onsite quality inspection
- Quality assurance
- Logistical consultation
- Supply chain support and solutions
- Trade management solutions
- Obsolescence solutions
- Economic, manufacturing, and operational feasibility analysis
Resource management and purchase:
Zoitech provides services for global component sourcing, purchase, and management using turnkey services via multiple EMS vendors throughout India.
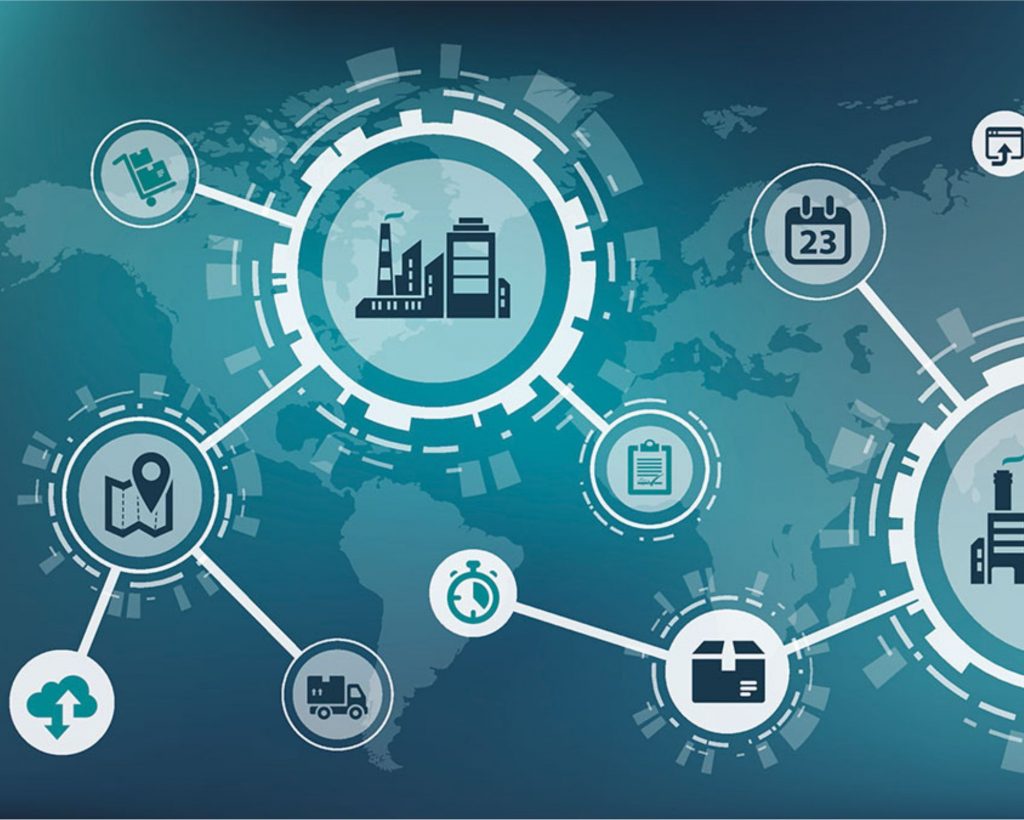
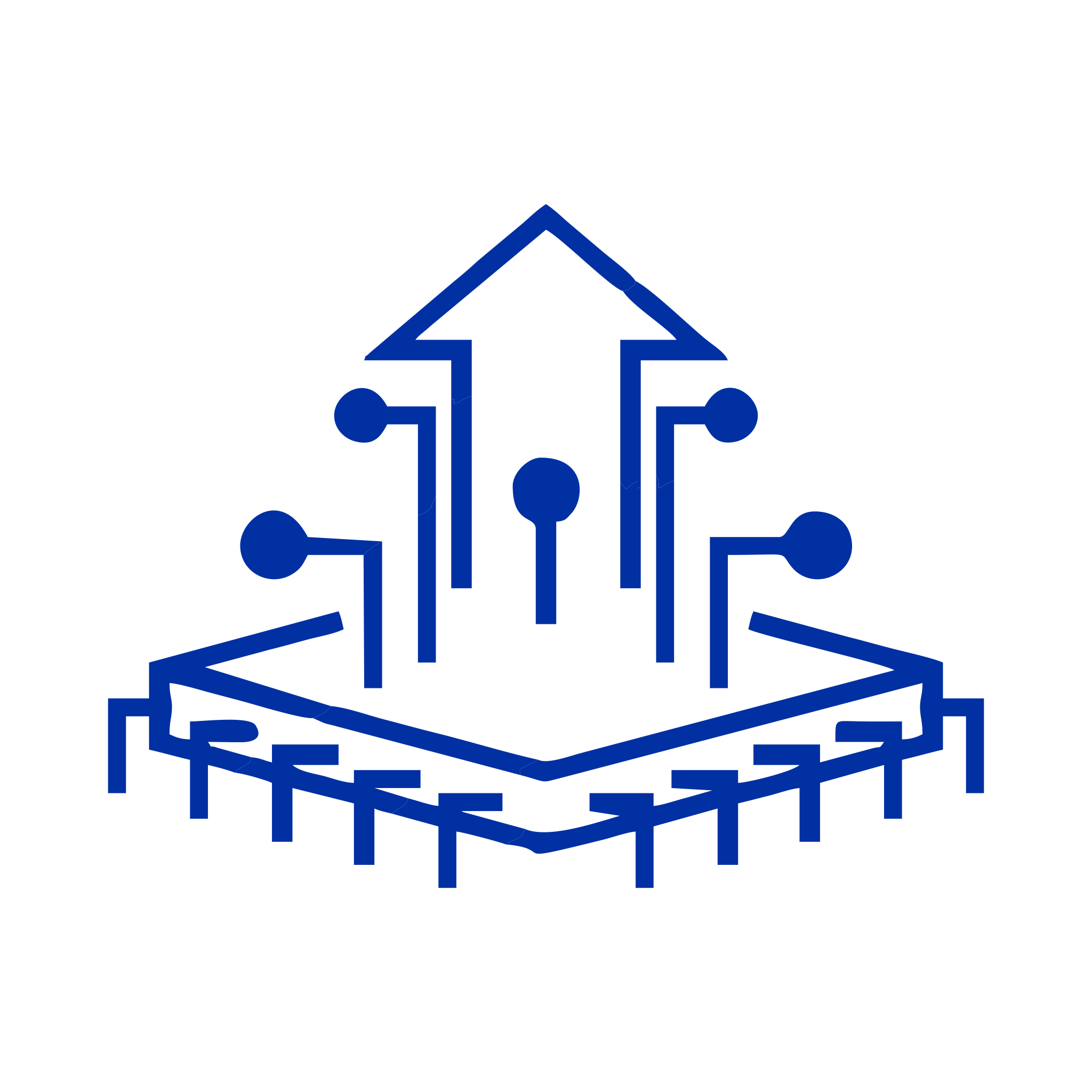
PCB Manufacturing :
Zoitech, through our various PCB manufacturing partners, provides PCB manufacturing services at an extremely competitive rate. Based on the customer’s demand a set of manufactures are selected for competitive quotes.
- Single-Sided PCB
- Double-Sided PCB
- Multi-layer PCB, up to 12 layers
- High-Frequency PCB
- Aluminum backed PCB
- Flexible PCB
- Rigid-Flex PCB
- Metal Core PCB
We work collectively with our clients to analyze and evaluate their requirements to offer tailored and premium quality printed circuit boards at the most competitive price and timely delivery.

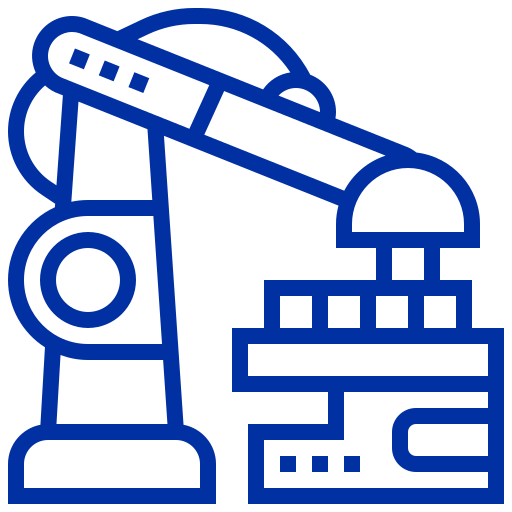
PCB Assembly :
We together with our various EMS (Electronic Manufacturing Services) partners, endeavor to meet the requirements of our client.
We provide following services:
- Material procurement and purchasing
- Material inspection and verification to avoid delays, rejects and rework.
- Supervised PCB assembling for pilot/test batch.
- Batch firmware/software flashing
- Design support for testing rigs and custom pogo pin beds.
- Wave, reflow and direct soldering.
- SMT and TH component rework.
- Ultrasonic cleaning of the assembled PCB
- Conformal coating
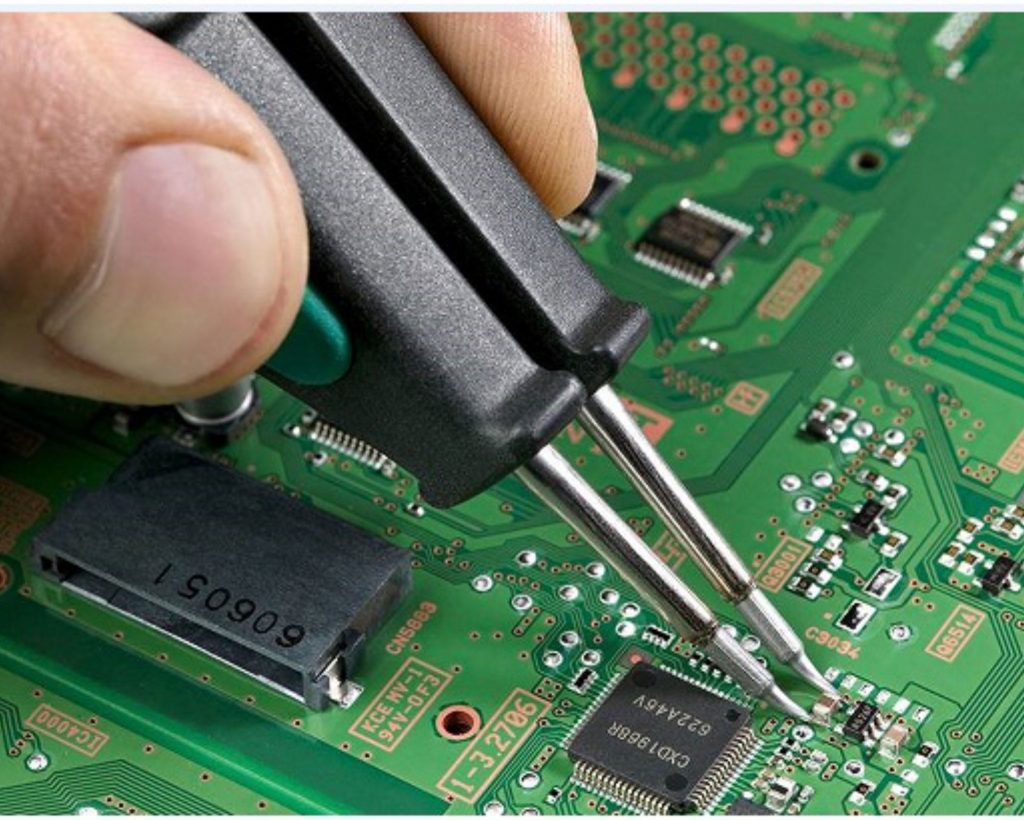
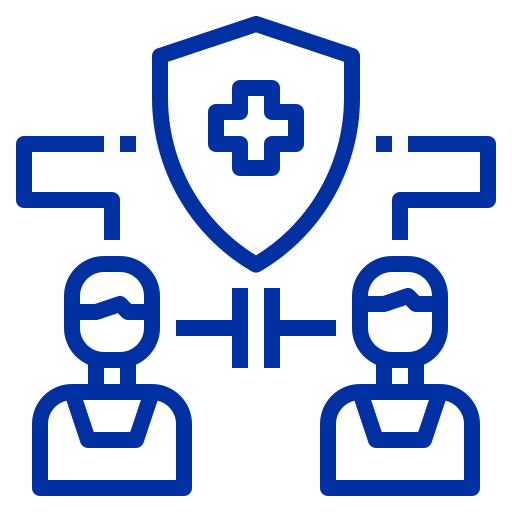
Calibration and testing :
As a part of Zoitech’s quality management, the company undertakes quality assurance at every stage of the product lifecycle to ensure quality and functional excellence. Zoitech adopts a practical and cost-balanced approach for Quality Testing and Quality Assurance throughout the quality management process to execute QA Automation, Functional Testing, Test Automation, Test Automation: Hardware In The Loop (HIL), and Verification & Validation (V&V) functions.
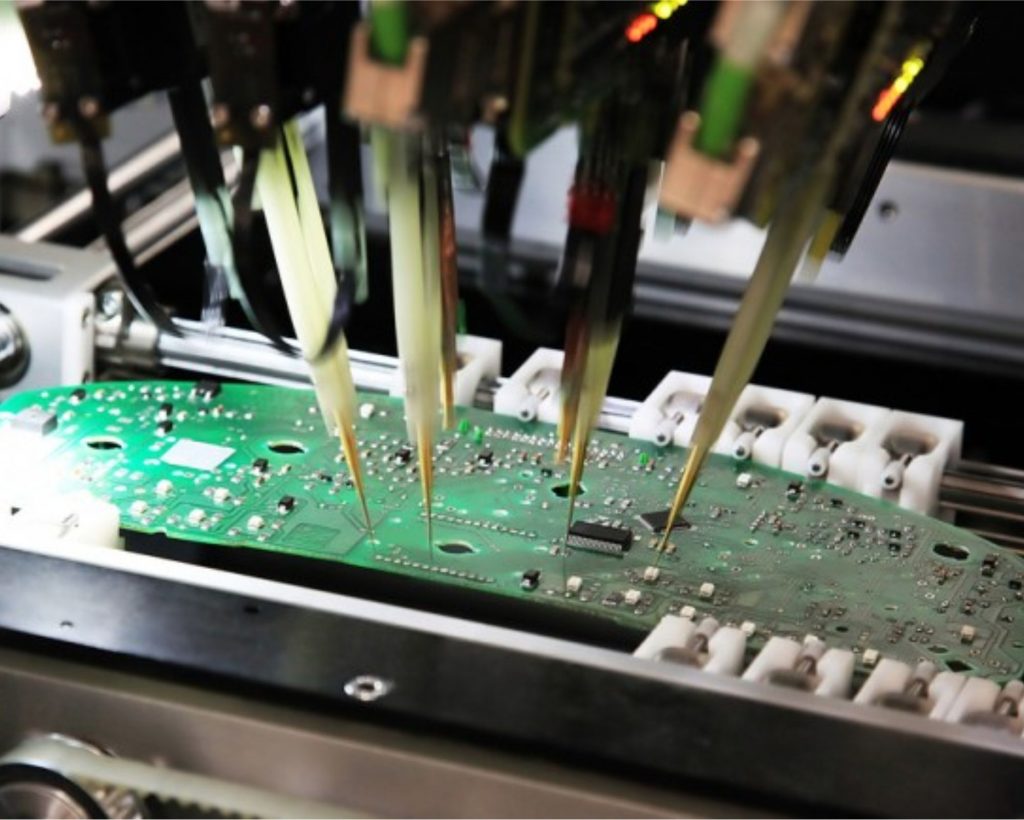
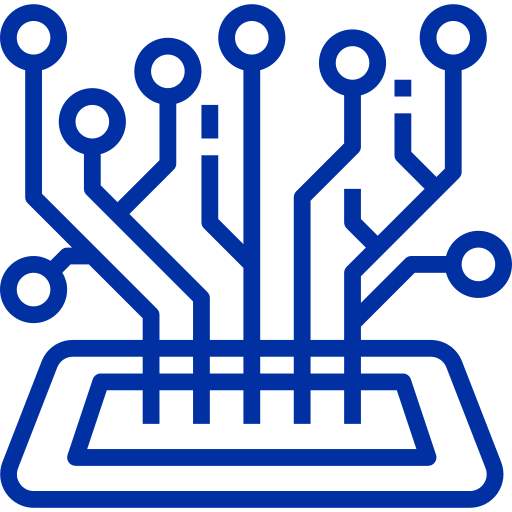
Enclosure design and mold making :
Zoitech Mechanical Design and Manufacturing solutions capitalize on its cost-efficient multiservice manufacturing facility and vertical design model. We conduct and manage the entire product lifecycle starting with mechanical design to prototype to pilot production and finally to economically efficient large-scale production.
We initiate final mold manufacturing after our designers complete the mechanical design to facilitate mass production. Our mold strikes a balance between design and durability. We finalize the design as per the client’s feedback and approval. The mass production commences once the client approves the design.
Zoitech designs affordable commercial and industrial enclosures with DFM (design for manufacturability) in mind. We, through our multiple partners, manufacture custom enclosures in materials like Plastics, sheet metal, Aluminum, Stainless Steel, and Mild steel for different types of an electronic system such as Radio, Power electronics, industrial and scientific laboratory equipment.
Besides the mechanics design service, we provide the following services.
- 3D rendering of the enclosure design
- Material selection based on application.
- Design tests such as fitting, stress analysis, and drop tests.
- Ultrasonic welding and adhesive selection
- Product packaging bulk and individual design
- Label and product manual design
- Logo graphic printing services on different surfaces
- Product marketing videos.
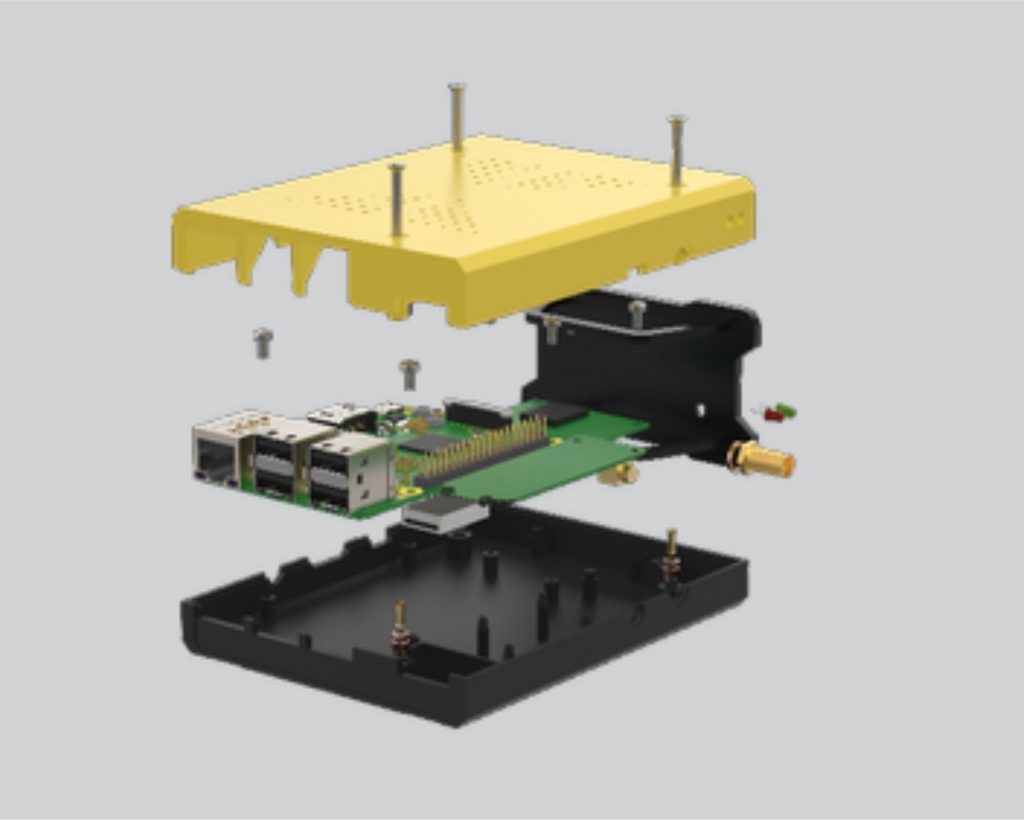
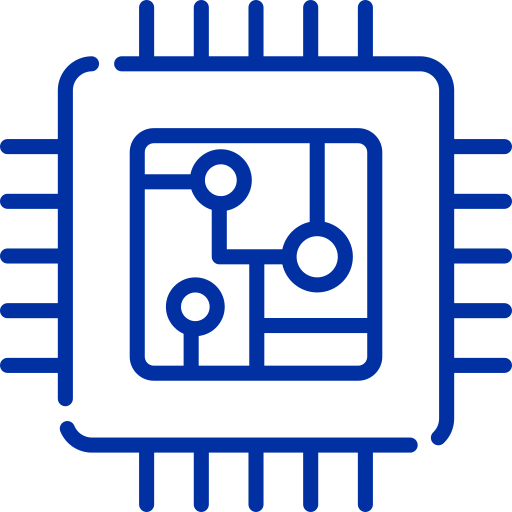
Prototype verification :
Before heading to mass manufacturing, it is important to verify the design for mass manufacturability. Following steps are taken to verify the manufacturability of provided electronic prototypes:
- Component availability and alternate parts
- Bill of material verification
- Assembly line compatibility.e., component placement and solderability
- Manual component assembly verification
- PCB panel design
- PCB cleaning and coating method
- PCB specific steps
Out of multiple design ideas drawn based on given electronic design, few are selected based on the client’s approval and verified for functionality and manufacturability using the following steps.
- DFA (design for assembly), making sure it is possible to assemble and disassemble (if needed) the product.
- 3d print the design for aesthetic, assembly, and function verification.
- Mold manufacturing verification
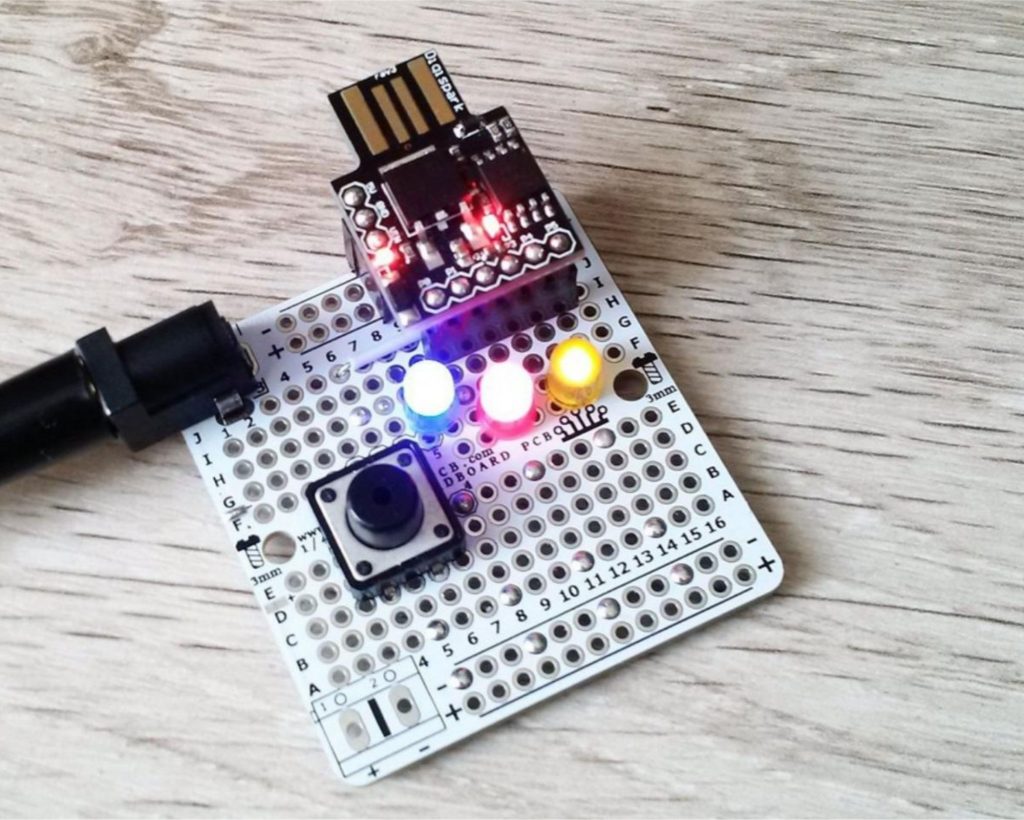
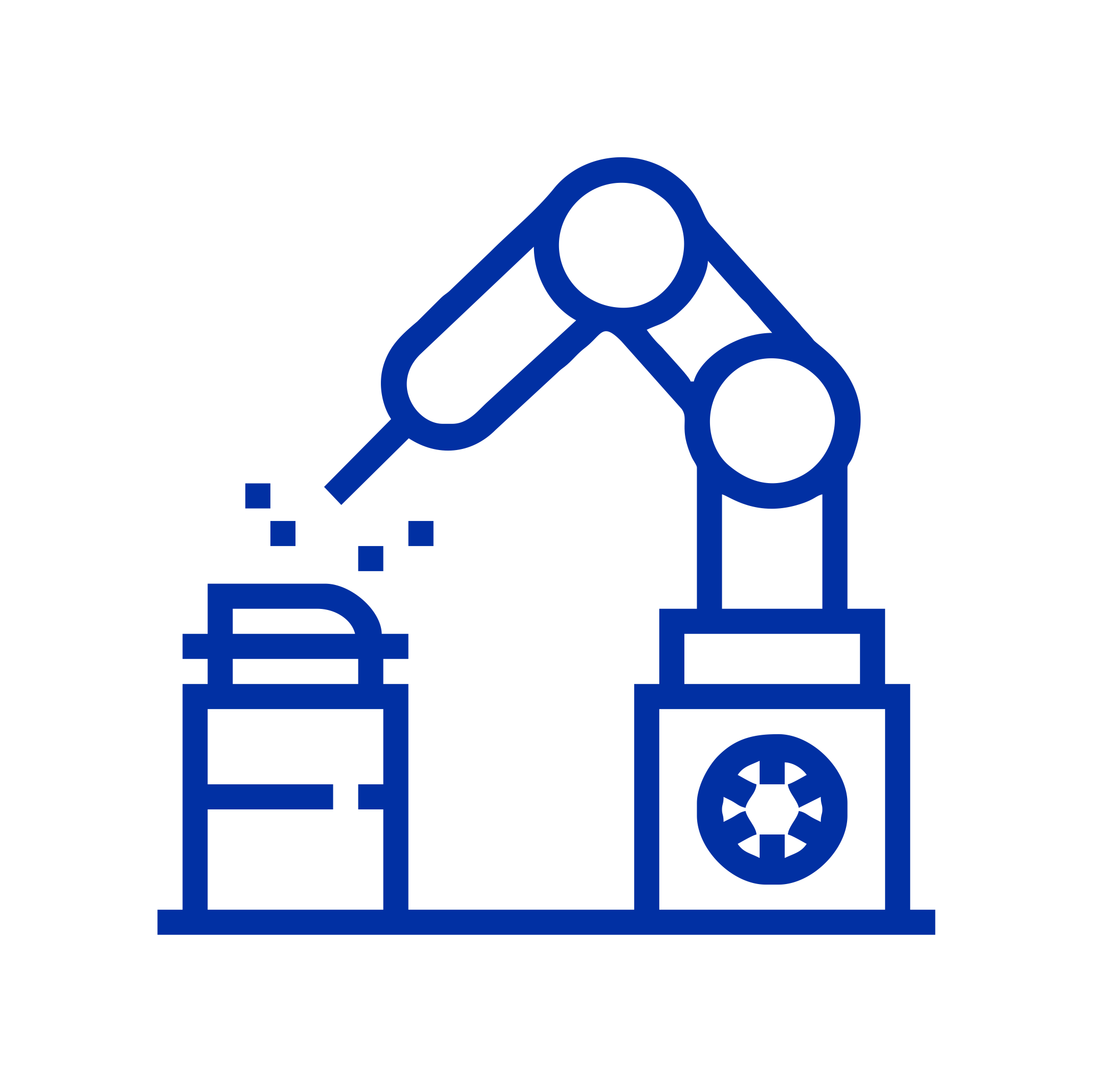
Product assembly and testing:
Product assembling and testing is the last step in the product line before labeling/printing and packaging. Zoitechforms assembly verification steps for mass manufacturability while working parallelly with the clients to add technical/functional tests to produce a quality product. The test pipelines can be modified as per the client’s feedback to improve the final yield.
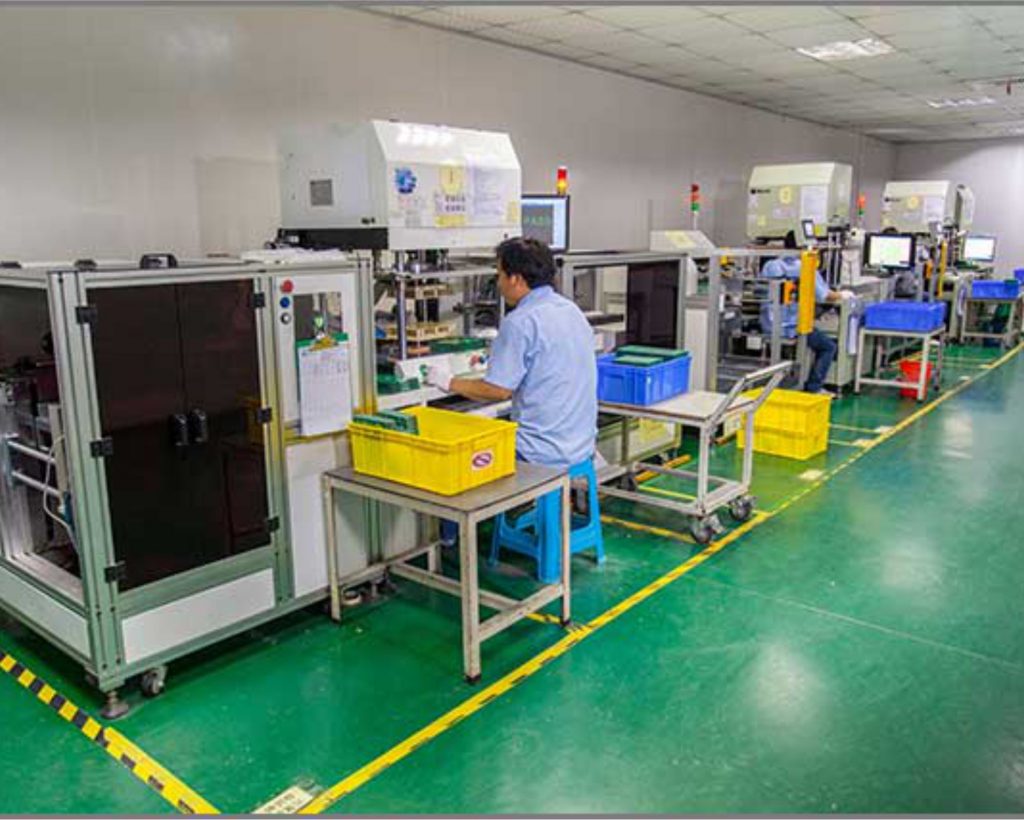
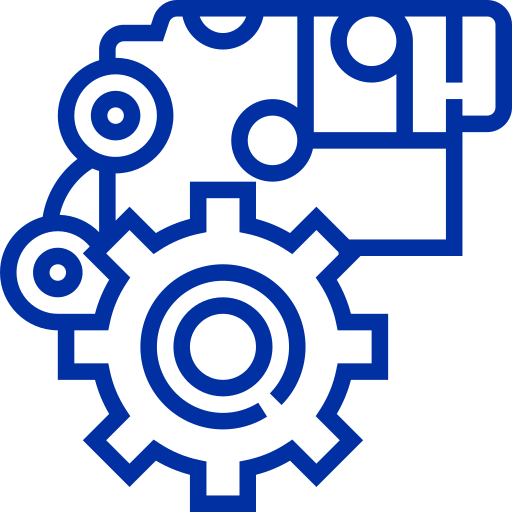
Pilot production run:
Zoitech recommends pilot run for any new products to set the manufacturing pipeline with proper assembly and tests setups. A pilot run helps the manufacturer and the client to see the throughput and adjust/allocate resources to improve different sections of the manufacturing pipeline as per need.
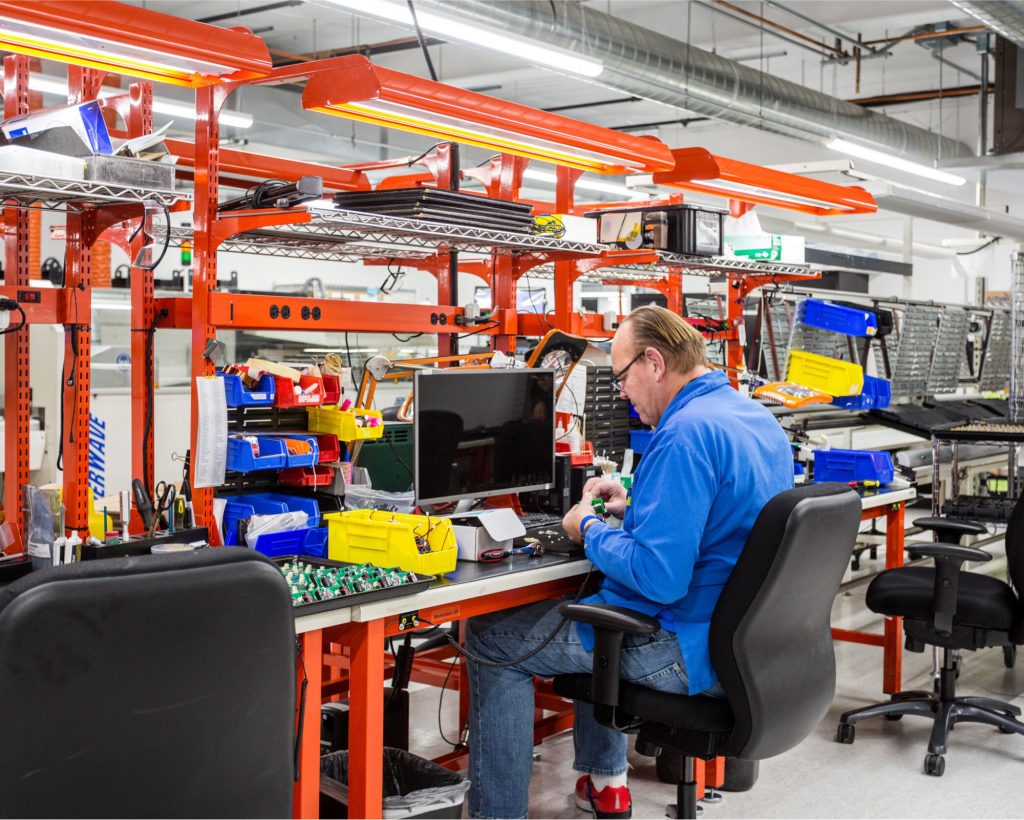
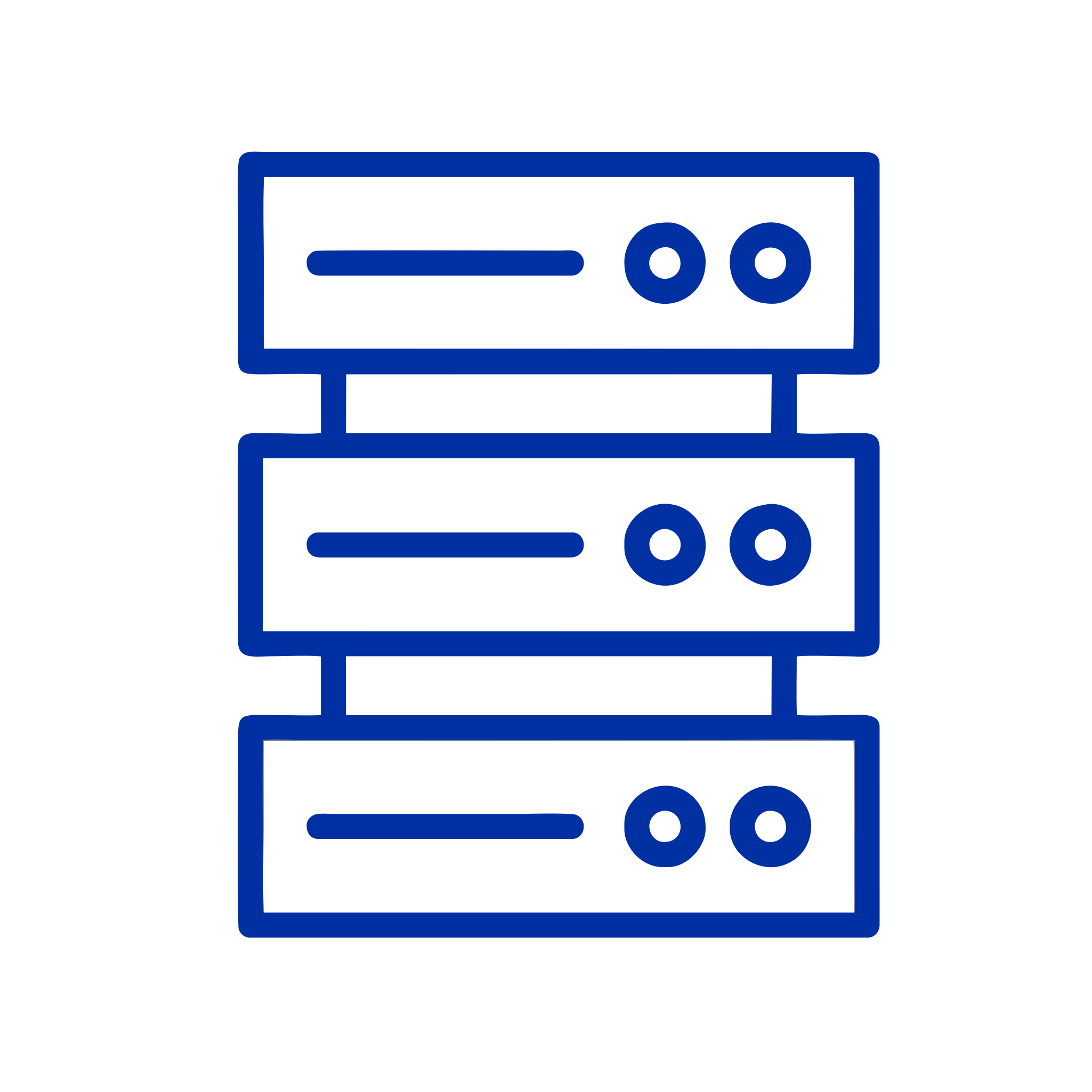
Storage :
We provide onsite storage facilities, inventory management and invoice forwardingservices to our international clients. These storage facilities are generally temperature and humidity controlled. Special storage services can be acquired upon client’s request.
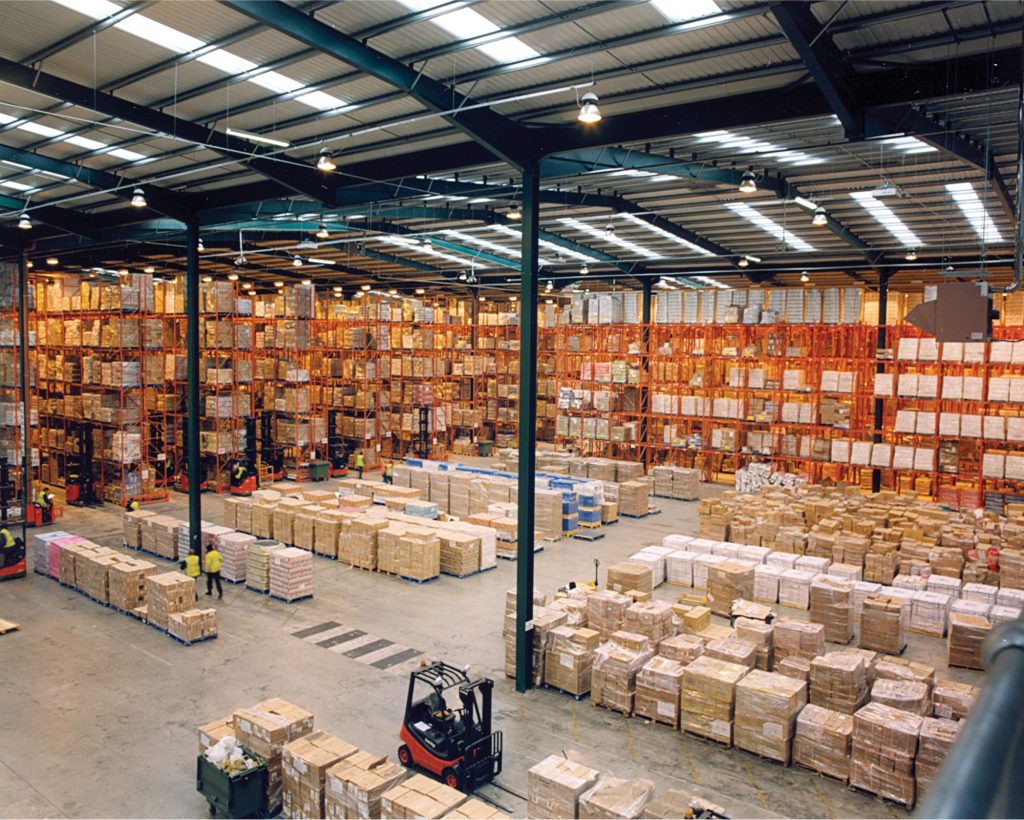
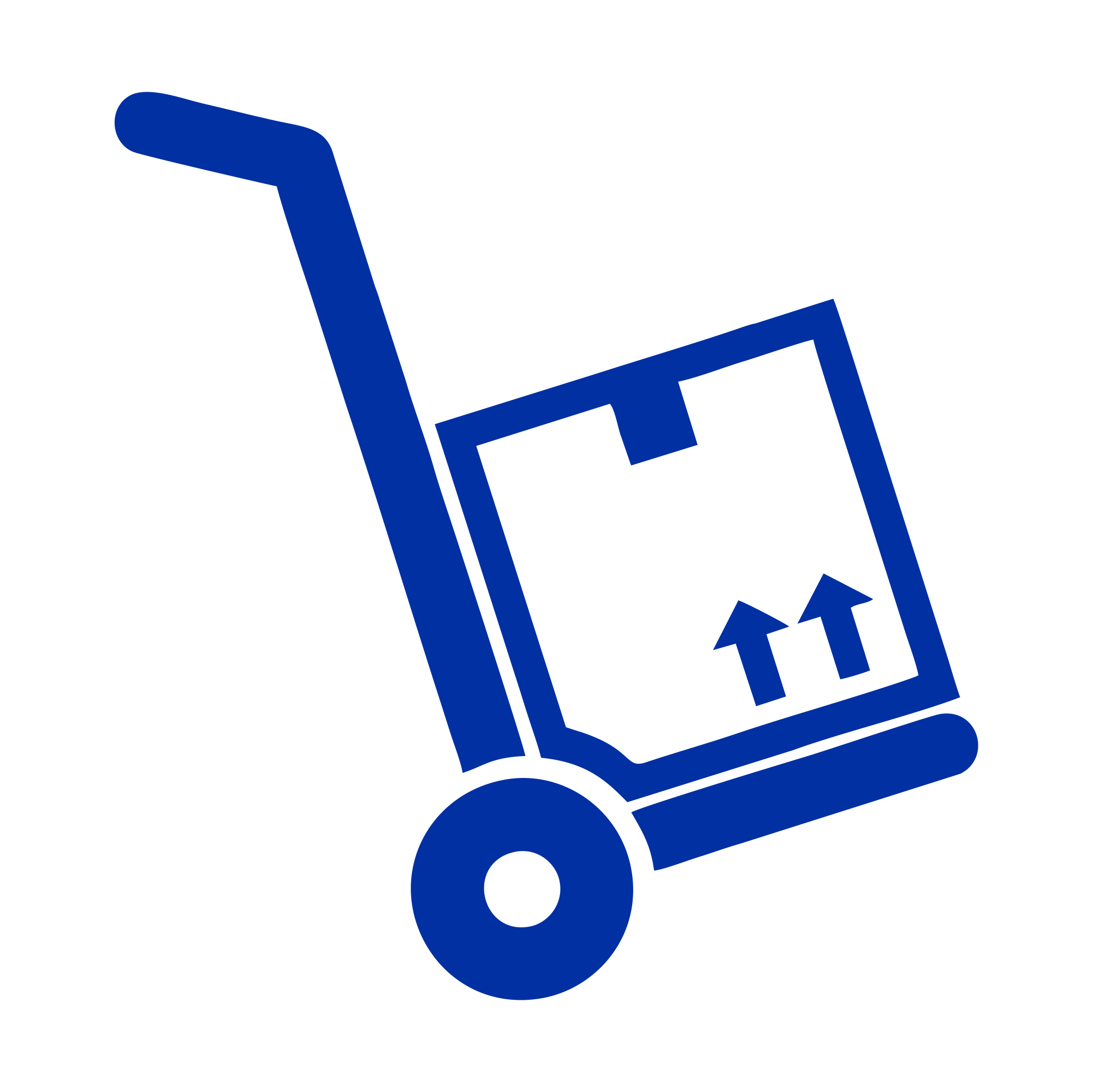
Logistics :
We ship manufactured products to our clients or any other requested destination worldwide using only reliable courier services such as DHL and FedEx.
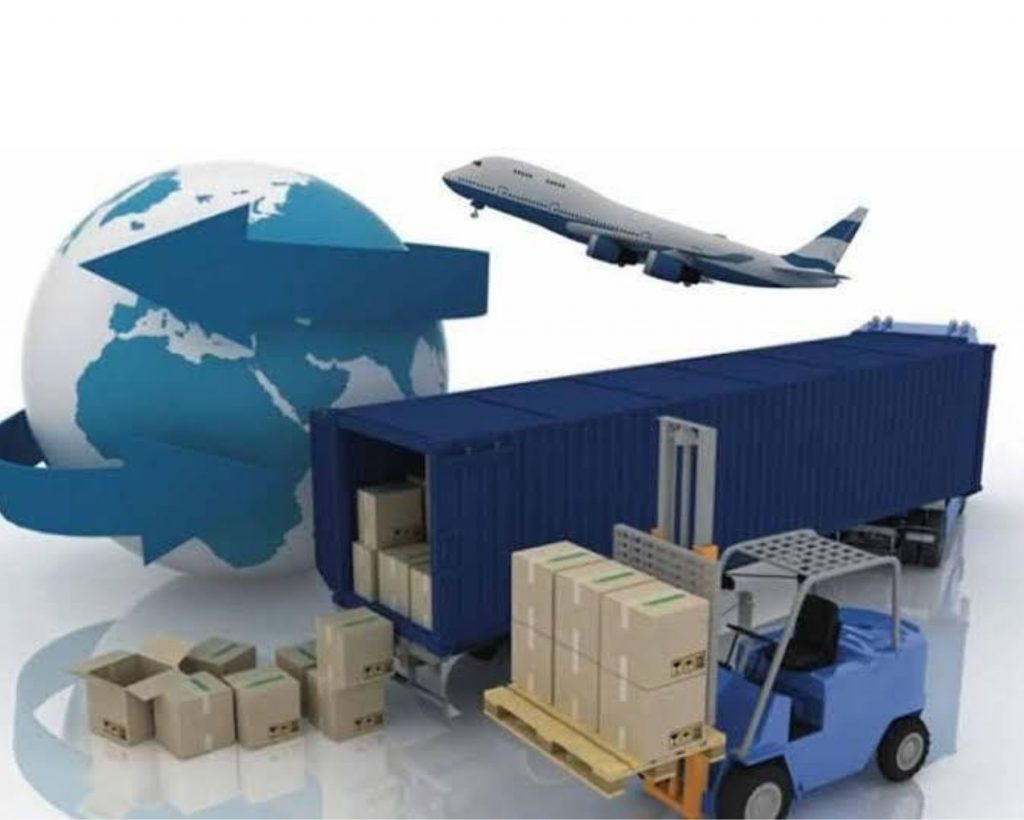